Professional Welding Inspection Milwaukee Solutions for Quality Control
Wiki Article
Just How Welding Assessment Contributes to Durability and Reliability in Construction Tasks
Welding evaluation offers as a foundational aspect in making certain the longevity and integrity of fabrication jobs. By methodically identifying possible defects during different phases of production, welding examinations not only avoid expensive failures yet also promote a society of high quality guarantee within the group.
Significance of Welding Inspection
Guaranteeing high quality with welding assessment is an essential component of any fabrication project. It serves as a safeguard to confirm that welding processes satisfy well established criteria and specifications, thereby boosting the total integrity of the structure or element being fabricated. Welding inspection is not merely a procedural step; it is a necessary method that assists determine possible problems early, making sure that they are dealt with before they rise into considerable issues.The relevance of welding inspection can be underscored by its duty in preserving safety and toughness. Welded joints are frequently subjected to severe conditions, and any defects can endanger the performance and longevity of the final item. By carrying out rigorous examination protocols, organizations can ensure conformity with industry guidelines, therefore lessening risks linked with structural failings.
Additionally, effective welding examination promotes confidence amongst stakeholders, consisting of customers and regulative bodies, that the project fulfills the greatest top quality requirements. This not just improves the track record of the fabricator however also contributes to lasting expense financial savings by avoiding rework and prospective responsibilities. Eventually, welding inspection is important to the success and integrity of fabrication tasks, strengthening the value of quality control in design practices.

Typical Welding Flaws
Welding defects can considerably undermine the structural honesty of produced elements, making their identification and rectification crucial. Typical welding flaws can be broadly categorized right into 3 types: geometric, metallurgical, and service-related.Geometric problems include concerns such as damaging, where the base metal is deteriorated beside the weld, and too much convexity, which can cause anxiety concentration factors. These issues can jeopardize the strength and resilience of the weld joint.
Metallurgical issues emerge from improper welding treatments or materials, leading to troubles such as porosity, where gas pockets create within the weld, and lack of blend, which happens when the weld metal fails to bond effectively with the base metal. These issues can substantially damage the weld's effectiveness.
Service-related issues may not emerge up until after the element remains in use. Instances include breaking due to thermal stress and anxiety or fatigue, which can bring about catastrophic failings if not attended to.
Understanding these typical flaws empowers makers to execute reliable evaluation strategies that enhance the dependability and long life of their tasks, inevitably making certain safety and efficiency criteria are met.
Assessment Methods and strategies
A comprehensive technique to assessment methods and methods is necessary for identifying and reducing welding flaws in manufacture projects. Various techniques are used to ensure the stability of welds, including aesthetic assessment, ultrasonic screening (UT), radiographic testing (RT), magnetic bit testing (MT), and color penetrant testing (PT) Each strategy has its strengths and particular applications.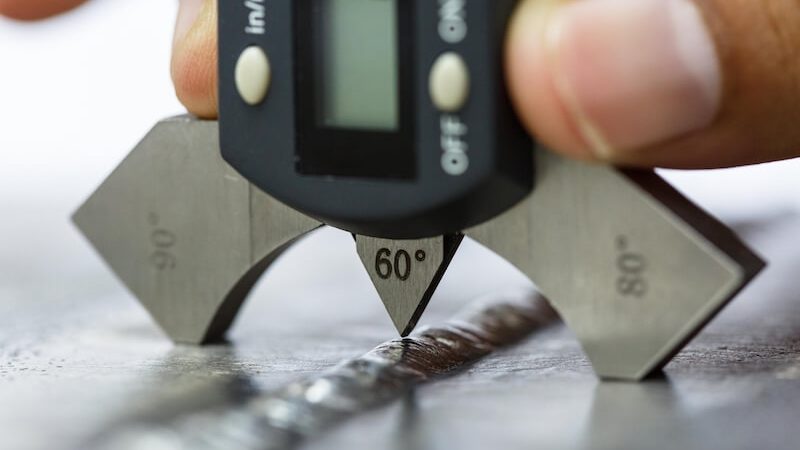
Magnetic fragment testing is beneficial for detecting surface and near-surface issues in ferromagnetic materials. By using an electromagnetic field and making use of ferrous bits, assessors have a peek here can identify interruptions effectively. Color penetrant testing highlights surface-breaking flaws via the application of a color that seeps right into cracks, making them visible under ultraviolet light.
Using a combination of these methods makes certain a rigorous assessment, enhancing the dependability of welded structures.

Effect On Job Durability
Efficient assessment methods considerably influence the longevity of fabrication projects. By recognizing possible flaws and inconsistencies in welding procedures, evaluations guarantee that frameworks are constructed to hold up against functional anxieties in time. When welds are thoroughly examined, the possibility of undiscovered concerns, which might lead to architectural failings, is decreased.Routine inspections promote adherence to market standards and policies, which are important for making sure the sturdiness of bonded joints. Such compliance not just improves the integrity of the job but likewise comforts stakeholders relating to the quality of the job. Prompt detection of flaws enables for rehabilitative activities to be taken early, preventing pricey fixings or complete overhauls down the line. Welding Inspection Milwaukee.
Additionally, efficient evaluation practices promote a society of quality control within manufacture teams. When employees know that their work will be carefully examined, they are more probable to stick to ideal practices and maintain high standards throughout the production procedure. Inevitably, this commitment to high quality not only extends the life-span of the job however likewise decreases upkeep prices, consequently improving the general financial stability of construction endeavors.
Enhancing Reliability in Fabrication
Integrity in manufacture is substantially enhanced with extensive evaluation processes that resolve possible weaknesses in welding techniques. Reliable welding assessment not just recognizes problems early however additionally gives essential feedback to welders, guaranteeing adherence to developed criteria and specs. By utilizing non-destructive testing approaches, such as radiographic or ultrasonic examinations, producers can determine the integrity of welds without endangering the material.Additionally, normal examinations foster a society of quality and liability among construction teams. When welders recognize that their work is subject to stringent analyses, they are more probable to follow best methods and methods. This proactive technique reduces the threat of expensive failures during the functional stage of a task.
Ultimately, enhancing reliability in manufacture via extensive inspection processes not just enhances the lifespan of the made components but also strengthens stakeholder confidence in the job's total high quality and durability. Spending in durable welding evaluation practices is crucial for achieving long-lasting dependability in any home kind of manufacture endeavor.
Final Thought
In recap, welding evaluation functions as an essential element in ensuring the longevity and dependability of fabrication jobs. By determining flaws early and utilizing non-destructive screening techniques, evaluations promote a society of quality control that adheres to industry requirements. The methodical documents of outcomes not only assists in trend evaluation yet likewise improves liability and structural integrity. Inevitably, efficient welding assessment methods reinforce stakeholder confidence and significantly contribute to the financial viability of fabrication endeavors.Welding evaluation serves as a foundational aspect in making certain the longevity and reliability of fabrication projects.Making certain high quality via welding examination is an go to this site essential part of any kind of fabrication job. Eventually, welding inspection is indispensable to the success and reliability of construction projects, strengthening the value of top quality guarantee in design practices.
An extensive technique to examination methods and approaches is vital for alleviating and identifying welding problems in manufacture tasks.In recap, welding inspection serves as a crucial element in guaranteeing the long life and integrity of fabrication tasks.
Report this wiki page